Specialisation in Web-Fed Digital Printing
CX1200e Digital Label Press And FX1200e Digital Finishing System
Case Study: Typographica GmbH – switching to narrow-web digital printing
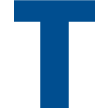
he printing industry is in a process of constant change. This is particularly true for label printing. Since much more is possible at the technical level nowadays than was only ten years ago, the quality requirements made by the packaging industry are of course increasing, too. Companies that want to succeed in this fiercely competitive environment need not only to move with the times but also to develop new ideas, to specialise and to fill niches. An advice especially true for smaller service provider, which wouldn't stand a chance against well-funded large printing companies. The owner-run family company Typographica from Pulheim near Cologne in Germany is a perfect example for a promising business model..
25 years ago, Peter Datum decided to become an outsourcing supplier in the printing field and established Typographica GmbH. In 1994, he was joined by his son Oliver Datum, who made major changes to the company's business. Until early 2010, they then focussed exclusively on pre-press operations. Most of the customers came from the chemical and pharmaceutical industries. However, due to new technologies and new machines, practically no customers had any more need for the films that had been standard in the past.
"That was also the reason why we started thinking about what needs our customers – including not only the packaging industry but also big printing companies – might have. We soon discovered that there needs to be a way to supply finished labels faster, less expensively and in higher quality depending on the number required," explains company director Peter Datum. The solution was web-fed digital printing.
The Datums began to look for appropriate technology and found the CX1200e narrow-web digital label press that Primera Technology had just launched on the market.
The machine satisfied the main requirements: it had to be possible to produce runs of several hundred or thousand labels without any intermediate manual operations. At the same time, the machine had to be able to produce shorter runs economically viably as well. The printing quality played a central role, too. The CX1200e prints in full-colour. And with the high resolution of up to 2,400 dpi finer graduations and more exact text and graphic settings are achieved.
An example: "The cosmetics industry has very specific demands on visual appearance. Some of the labels we manufacture are shown in TV commercials. With the new machine we can meet these requirements without any difficulties," adds junior director Oliver Datum..
Rising requirements satisfied
With the help of the digital laser printing process, the CX1200e processes up to five metres of label material per minute, depending on the quality settings. The extra high-capacity toner cartridges have a printing capacity of 4,600m with a web width of 216 mm (estimated at a toner density of twenty per cent). "We are now able to print longer label formats. We are talking here about up to 1,000 mm – and that on rolls! There's no other machine in Germany that can manage that," mentions Oliver Datum. The ingenious winding and clamping system automatically applies the right amount of pressure to the output roll with the labels that have already been printed. Therefore, separate winding of the roll is not necessary. Further to that, a software tool indicates during proof printing what the costs per label are. "Thus, our cost estimation process is more reliable than it has been in the past," explains Peter Datum. The CX1200e demonstrates flexibility where substrates are concerned: the user can choose between laser printing paper, white and clear polyester and vinyl – with the extra options of matt, semi-gloss or high-glossy finishes.
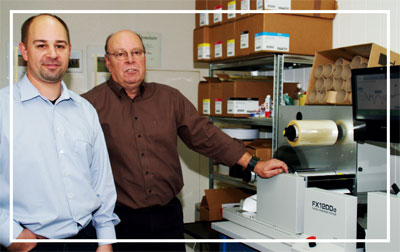
The senior assumes that the costs of the two machines
are charged off within a maximum of two years.
"Finisher" completes solution
Shortly after the digital colour label press, Primera Technology also presented the FX1200e digital finishing system. "By doing this, the manufacturer offered us a complete production line that does everything from printing and conversion to coating, digital die-cutting, slitting, rewinding and even automatic waste disposal. And both machines are co-ordinated perfectly," Oliver Datum points out. What is known as QuadraCut technology, for which a patent application has been filed, makes sure the punched waste is removed from the finished labels tidily. About 6.10m are die-cut and finished within a minute. Four tungsten carbide pivoting knives are in operation simultaneously during this process, which increases the throughput significantly in comparison to machines that operate with just one blade. Because of the used material, Typographica does not need to have extra plates and dies produced or replaced any more either. As a result production stops can be avoided. The edging removed from the labels is immediately rolled up by the FX1200e, so that waste disposal is no problem. "Another special advantage of the finisher is that we can cut any label shape, even when there are cut-outs in it", Oliver Datum continues. There is a large application for that in the chemical industry, where manufacturers and traders of chemicals as well as packaging service providers are required to comply with the new GHS regulations and have to stick completely redesigned hazard pictograms on their products.
New solution is generating more and more business
Since the CX-FX combo system started operation, printing already accounts for about forty per cent of all the work processes at the company. Apart from pharmaceutical and chemical companies as well as cosmetic manufacturers, now producers of food supplements and large printing companies are among Typographica's new customers. "With the two Primera machines we have defined a new business area, expanded our portfolio and very successfully filled a niche," says the company founder.
It goes without saying that not just quality criteria but also economic factors have to be taken into consideration. "For instance, classic printing machines need a certain number of labels to 'warm up', which is not the case with the digital colour label press. If a customer needs 100 labels, I still have to produce 500 when using the classic printing process. The CX1200e can even produce one single label without any waste or financial losses," Peter Datum stresses. Important economic factors are the size and design of the label in relation to the quantity. The time and manpower required also adds to that. The advantages of the FX1200e become very clear here, since the labels are cut, slit and rewind automatically. Typographica also claims to be faster than other suppliers which opt for conventional printing processes for label runs of up to 10,000 labels. The company was enthusiastic about the relatively low purchasing costs of the two machines. Further to that the management of Typographica was especially satisfied with the support from Primera and One Point, distribution partner of the manufacturer.
According to both Peter and Oliver Datum, by now the company has made a name for itself with its specialised printing service. Typographica already increased sales by about ten per cent. During the current year It's planned to acquire even more new customers. If they are successful, father and son are already considering the installation of a second finishing system.
DTM Print GmbH: Mainzer Strasse 131, 65187 Wiesbaden/Germany, dtm-print.eu , E-mail: sales@dtm-print.eu
One Point Storage Systems GmbH: Am Kuemmerling 21-2,
55294 Bodenheim/Germany, www.onepoint.de
Typographica: Rurstraße 2,
50259 Pulheim/Germany